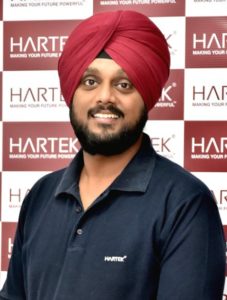
Hartek Group is a specialist in providing EPC solutions for substations and transmission lines up to 400kV. Recently, the group landed its first order for a gas-insulated switchgear (GIS) substation in Haryana. In this exclusive exchange with T&D India, Simarpreet Singh tells us how GIS-based substations are technically superior to their air insulated counterparts, not just in terms of technology but also from the perspective of EPC contractors.
What is the basic difference between AIS (air insulated switchgear) and GIS (gas insulated switchgear)?
While GIS uses sulphur hexafluoride (SF6) gas, which is five times heavier than air, AIS is based on air insulation in a metal clad system. Installing GIS is faster and easier since GIS systems are significantly smaller and lighter as compared to AIS.
GIS systems are also easier to maintain on a regular basis owing to their front access. They generally need to be inspected every four years or so depending on the specific manufacturer recommendations of the device. GIS drives need to be re-greased after about 20 years. AIS systems, on the other hand, have to be inspected every one or two years.
Talking in terms of the cost of ownership, the upfront costs of GIS and AIS must be weighed against the lifelong maintenance these devices demand. GIS units tend to cost 10-40 per cent more than AIS devices. The minimum lifespan of switchgear systems is 30 years.
What technical advantages that GIS offers over AIS?
GIS systems save a lot of space. GIS substations take up only 10 per cent of the space that a conventional (air-insulated) substation occupies. SF6 has superior dielectric properties when used at moderate pressure for phase-to-phase and phase-to-ground insulation. Arc flashes are rare in GIS as all the interior elements are insulated.
What advantages does GIS offer to EPC contractors, over AIS?
The cost of GIS may be more, but it offers a higher return on investment. GIS scores over AIS both in terms of upkeep and installation time. GIS systems are not only much faster and simpler to install, they are also quite easier to maintain. But we, at the Hartek Group, believe that no matter what the technology is, the success of a substation project hinges on finer aspects of design, engineering and installation with high quality standards being the cardinal principle.
GIS uses SF6 (sulphur hexafluoride) that is considered environment-unfriendly. What is your view?
So as to ensure environmental and personal safety, we should make it a point to adopt certain system design standards which minimise pollution, like hermetically-sealed gas compartments and provisions for gas recycling and disposal. Effective handling policies, both during maintenance and final disposal, can go a long way in addressing the issue.
Are there any challenges that EPC contractors face during the execution of projects involving GIS?
One of the major challenges before us is looking for ways to reduce the cost of constructing new GIS facilities and retrofitting them as technology evolves. But to be able to do that without compromising on reliability and overall quality poses an even bigger challenge. Executing GIS substations in difficult urban locations can also be a formidable task.
Hartek recently forayed in the GIS substation EPC space. Tell us more.
Hartek Group recently bagged its first-ever GIS project of 132kV from the Haryana Vidyut Prasaran Nigam Ltd (HVPNL), which will be constructed in Jhajjar. We have been targeting GIS-based projects for the past two-three years as we feel the need to move towards newer technologies to create a smart power infrastructure for the country.
Does GIS have any specific technical advantage when it comes to T&D infrastructure for solar power plants?
From an EPC contractor’s point of view, executing GIS substations for solar plants can save a lot of time, which is of utmost importance when it comes to renewable energy projects. Otherwise, GIS offers by and large the same advantages for both solar and conventional substation projects.
What is India’s level of self-reliance when it comes to key equipment used in GIS-based substations?
India is fairly self-reliant in GIS-based substation technologies. With GIS-based substations expected to come up on a large scale in the near future, Indian companies are ready to cash in on the emerging trend. Many of these companies have already tied up with foreign multinationals to make their presence felt.
Apart from multinationals operating in India, do you see homegrown companies supplying GIS equipment?
Absolutely! Though domestic manufacturers in the GIS equipment market face stiff competition from foreign multinationals, they have demonstrated time and again that they are second to none in terms of quality and reliability. India has the resources and capability to manufacture complex products and come up with technological innovations. Indian manufacturers should come up with indigenous technological advancements by emulating MNCs who have developed world-class products over the years, by investing heavily in R&D. The “Make in India” campaign should emphasize on technological applications and encourage homegrown companies to take the lead in GIS technology and practices.