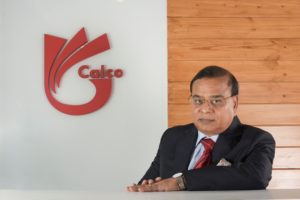
Part of the diversified Calco Group, Calco Poly Technik is a global player in the field of high performance engineering plastic catering to the automotive, electrical and electronics industry. We have Vijay Kumar Gupta discussing in detail the role of plastic in the electrical equipment like switchgear and lighting devices. With increasing adoption of environment-friendly polymers, Gupta feels that conventional heavy metal parts are being rapidly replaced by plastic, giving benefits of higher productivity and lower cost of production.
We understand that Calco Poly Technik supplies high-performance plastics to the electrical equipment industry. Take us through the products that you supply to.
Our product range covers diversified product range in conventional and new technology space. Our PiCAN range of polymer covers all aesthetic product range like switches. For switchgears we have CiLON range of products for flame retardant and high performance. We also have developed new product range to help replace CFL with LED’s. You will also find our range of ZiLITE products for LED housing that manages thermal heat for long term performance. We also have new diffusor range in PiCAN that meets optimum diffusion/transmittance for varied applications in bulbs and tubes.
We are also working simultaneously to create sustainable solutions in electrical industry by innovating with light-weighing, environment-friendly and recyclable material.
Calco, as we learn, is opening a new plant in north India. Tell us more.
Yes, we plan to start our plant at Sonepat in Haryana by the end of 2018 with a production capacity of 20,000 tonnes per year. This will be one of the biggest capacities in India for high performance polymer. This unit is designed to run at high production speeds that will be capable to handle materials with integrated automation systems. Not just this, this unit will be most energy efficient with clear energy consumption through captive solar power generation. We plan to extend our existing range with new polymer compounds in PPS, PEEK, ASA, POM. This unit will also have the lowest carbon footprint in the industry.
Tell us about your R&D set up and the continual product engineering development of your products.
We have a team of experienced polymer and chemical engineers having extensive experience in different product applications. They bring with them over 50 years of rich experience in product testing and innovation. Equipped with all latest technology, they are continually working with our application development team and customers to identify opportunities in changing consumer expectations.
What is India’s import dependency as far as raw material for high-performance plastic is concerned?
India is a relative small market in the $67-billion global high performance polymer industry. Thus, all raw materials from high performance plastic are imported. You can see several multinational companies that have started their commercial activities by having local office in India or planning investment strategy for manufacturing in India. This industry will be supported heavily by ‘Make in India’ scheme, only if foreign investors see India holding a competitive edge over other Asian countries.
In electrical equipment, it is usually the product or the brand that gains prominence. As far as the consumer is concerned, there is little awareness of critical inputs like plastics that go into the product. Tell us about the criticality of high-performance plastics used in various electrical equipment.
That holds true for any intermediate material industry. But the fact is these industries are the very heart of consumer goods. Brand is only the designer of the product. Technology and performance is defined by the domain expert of that very product. In our case, plastic is the face and the heart of product. Plastic gives your aesthetic appeal with color, gloss. It gives you the ability to form any shape. This is a byproduct of performance that plastic offers; it keeps you out of trouble during any fire, it gives strength with reinforcement materials for durability, in heat sensitive applications like lighting our materials gives excellent thermal conductivity. In short, we help make your life beautiful, safe and strong.
Can the selection of plastic affect the energy efficiency of electrical equipment? Please discuss.
Primary energy demand in India is around 1,500 million ton equivalent of oil by 2030. This will put economic pressure on imports bill. One way of reducing our dependency on energy requirement is making energy efficient equipments. Fundamentally this is possible by minimizing losses of energy transmission and increased conductivity, both thermal (heat) and electrical. Traditionally, plastic is poor conductor of thermal and electricity. They have found limited use in electrical equipment due to their unwanted behavior. With polymer modification, we have developed thermal conductive material that can dissipate higher Watt per sqm. This technology has significantly improved energy-efficient use of LED with low energy consumption. Similarly, modern panel displays and solar cells are all created by use of high conductive plastic. These components are integral part in efficient electronic circuit for better ratings of electrical equipments. Plastic thus plays a very pivotal role in defining a sustainable roadmap for efficient equipment.
Please tell us more about your plans of catering to more products and companies in the electrical equipment space.
We are always looking to collaborate with OEMs in electrical space to meet challenging demands and stricter government norms. We have created wide range of environment friendly flame retardant polymers that can replace conventional heavy metal materials in applications such as MCB, MCCB. In addition, they also offer low smoke preventing choking in case of fire. We are also working with leading lighting OEM to make affordable LED product range in downlighter, bulbs, tube which has potential to replace all existing incandescent light bulbs/CFL. You can soon see complete housing assembly made of plastic replacing metal giving benefits of higher productivity and lower total cost of production.
Our technologies can see light of day only if brands are willing to upgrade their products in line with international standards.